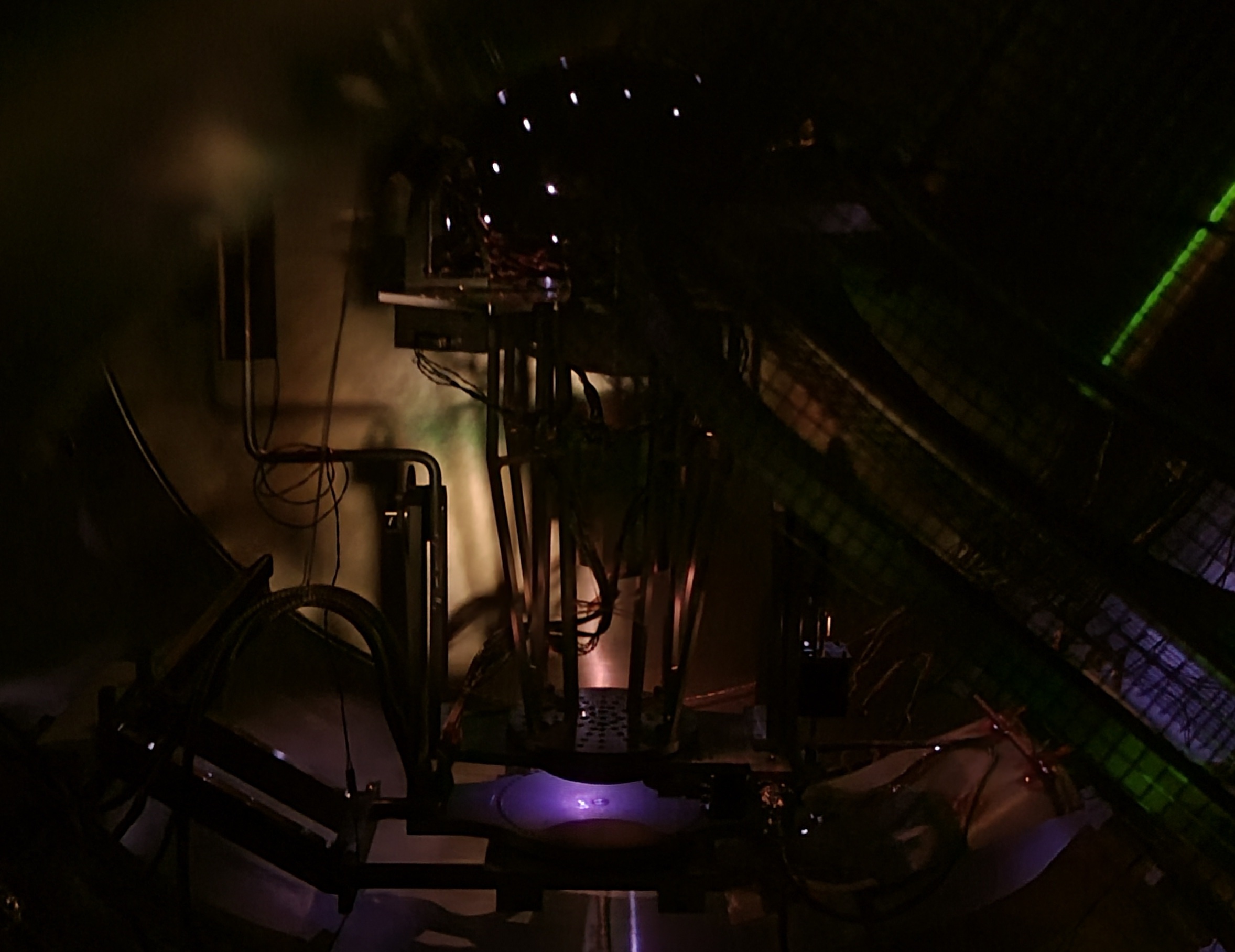
Generating Space Plasmas
Both types of rocket instruments I have worked with measure properties of space plasmas. This requires a
laboratory environment that can provide, not just a plasma, but one sustained at an ultra-high vacuum with
pressures of around a millipascal.
To create this vacuum, our lab uses a cryogenic vacuum chamber called
The Elephant, which
has a base pressure of around a micropascal, and an operating pressure of less than millipascal. Mounted to
this chamber is a plasma source which uses a magnetron, like the ones found in everyday microwave ovens, which
radiates microwaves through a quartz window, via a waveguide.
On the other side of the quartz window is a microwave resonant cavity into which various gases, such as helium,
nitrogen, or argon, are bled through a needle valve. Once in the cavity, these gases ionize by resonating
with the microwaves that are tuned to 2.45 GHz, matching the TE112 mode resonance design frequency.
Interfacing this cavity and the chamber is a backplate with 21 holes that are just large enough to seep the
plasma through while fully reflecting the microwaves. This ensures the microwaves do not interfere with the
experiments in the same way you can see your food heat up through a microwave oven window! The photo here shows
an argon plasma diffusing through the backplate.
The design of The Elephant was spearheaded by Kristen Frederick-Frost and it became operational in 2005. To
learn more, please give her
Ph.D. Thesis
a read!